The aviation agency of USA – the Federal Aviation Agency (FAA) – last month approved the biggest commercial jet engine in the world. The huge thrusters that it certified are the GE9X engines, one of which hangs under each wing of Boeing’s new widebody 777x aircraft. That plane flew for the first time back in January, and boasts folding wingtips – when they’re folded down for flight, they make the wings longer and thus more fuel efficient, and when they’re folded up, the plane will occupy less space at an airport gate.
These are the peculiarities in this mega jumbo jet engine:
1,05,000 pounds per engine
Each engine can produce 105,000 pounds of thrust for a total of 210,000 pounds. (The engine has even hit 134,300 pounds of thrust, a record.) But Pat Donnellan, an engineer on the GE9X engine program, says that pilots probably won’t need to max the engines out to get off the ground. In fact, maxing the engines out for lift-off is known as a “full-rated take-off,” he explains, but there’s no reason to do that unless you need to.
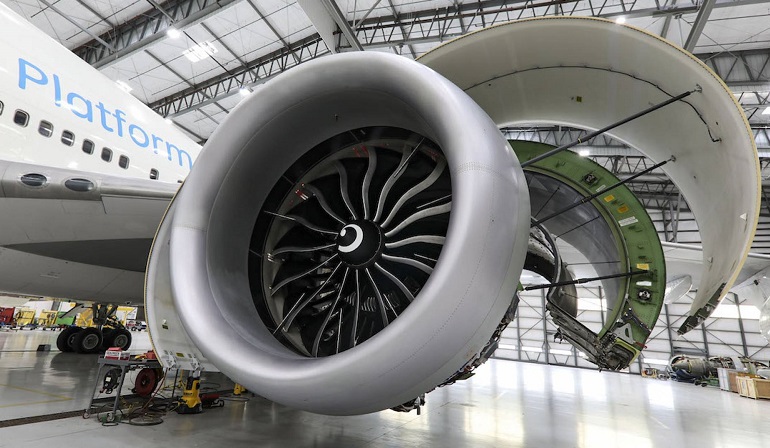
“You want to conserve as much of the life as possible, and not tear up an engine,” he says. He compares it to driving: Ideally, you’re not flooring the gas unless you really need to. More typical lift-offs are called “derated take-offs,” Donnellan says, in which “they use the right amount for the load that they’re carrying – the number of passengers and cargo.”
134 inches fan
The blade-to-blade tip diameter of the fan is 134 inches. That 11-foot span means that if you stand in the front of the engine in its front case (an activity best done when the plane is on the ground, with the engine off), you’d have plenty of headroom. That fan is the star of the show when it comes to producing thrust. “With the 777x being larger, we needed an engine that would provide the thrust level that the airframer wanted,” Donnellan says, referring to Boeing, “but at a much more efficient capability.” “To get there with a turbofan engine,” he adds, “you want to make the fan larger.”
16 blades
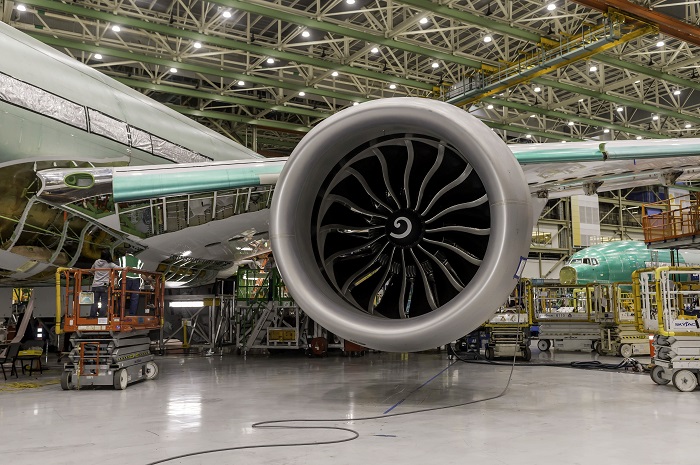
The curvy carbon fiber blades that constitute the spinning fan are fewer in number than they used to be. The engine’s ancestors, the GE90 and GENX, employed 22 or 18 blades. These new ones can produce more lift, and that’s because of design tweaks. “It’s got a wider chord to it—from the leading edge to the trailing edge,” he says. (“Chord” is a common wing measurement term.) “It’s got a little more twist in the proper areas, to generate that extra lift when we need it,” he adds.
2400 degrees inside engine
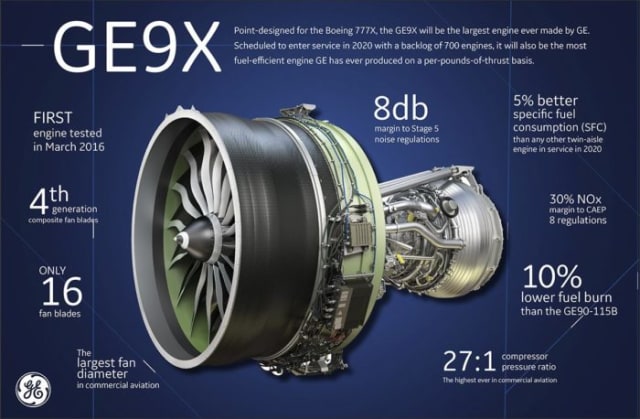
The guts of a turbofan engine are complex, but major components include the low-pressure turbine, the high-pressure turbine, the core, and the compressor. Air in the compressor, as you could imagine, gets compressed. “What you’re trying to do is drive the air down to the smallest amount, the smallest package, that you can,” Donnellan says.
“You’ve got a lot of energy now in that small package, and then you put that into the combustor.” Fuel enters the equation. “You ignite the fuel, which causes that small package of air to now get very big, very fast, and it will go through the high-pressure turbine.” That turbine harvests that energy, and some of that energy then fuels the low-pressure turbine, which powers the fan in the front.